In our exploration of the latest offshore wind farm building methods, we emphasize floating foundations, such as semi-submersible and spar-buoy designs, that support turbines ranging from 18-MW to 20-MW in deeper waters. We’ve found that Cold Fusion Concrete (CFC) markedly reduces carbon footprints by up to 90% while offering remarkable longevity, and advanced slip-form techniques enable continuous, rapid construction at rates of up to 100 feet daily. Additionally, innovations like jetting techniques minimize underwater noise, enhancing marine life protection. These methods demonstrate a transformative approach to sustainable energy production, and further insights follow on optimizing these advancements.
Key Takeaways
- Floating foundation technologies, such as semi-submersible and spar-buoy designs, enable deeper water installations for larger turbines (18-MW to 20-MW).
- Cold Fusion Concrete (CFC) offers lightweight, waterproof, and environmentally friendly construction with a lifespan in millennia and a 90% reduction in carbon footprint.
- Innovative slip-form construction techniques allow for continuous pouring of CFC, achieving production rates of up to 100 feet of structure per day.
- Advanced anchoring systems, including CFC chain/gravity and suction caisson anchors, enhance the durability and stability of offshore wind farm foundations.
- Low-noise installation methods, such as patented jetting technology, significantly reduce underwater noise, ensuring minimal disruption to marine life during construction.
Offshore Wind Farm Foundations
When it comes to constructing offshore wind farms, the foundation is essential for stability and longevity. Recent advancements have led us to innovative semi-submersible and spar-buoy designs, capable of supporting 18-MW to 20-MW direct-drive wind-turbine generators, strategically placed 50 to 100 miles offshore. These foundations are projected to last for millennia, drastically reducing maintenance needs and promoting a sustainable offshore industry, including hydrogen production. The use of advanced materials like Cold Fusion Concrete (CFC) not only extends lifespan but also reduces carbon footprints by 90% compared to traditional concrete. Additionally, innovative anchoring systems, such as CFC chain/gravity and suction caisson anchors, are recommended for their efficiency and durability, effectively managing multiple mooring lines over an impressive lifespan.
Advanced Construction Materials
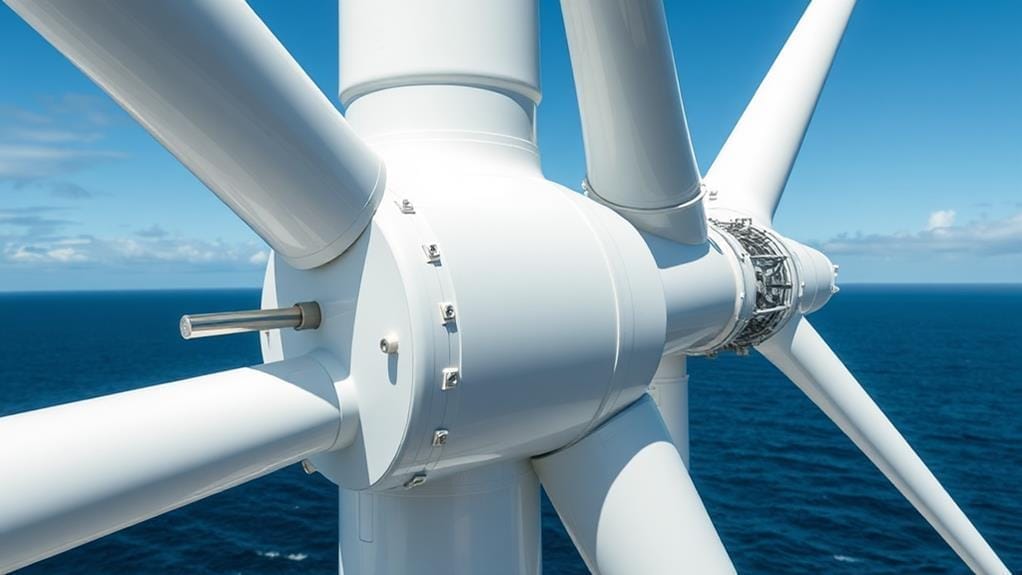
As we explore the construction of offshore wind farms, the choice of materials plays a crucial role in ensuring durability and sustainability. Advanced construction materials, like Cold Fusion Concrete (CFC), greatly reduce the carbon footprint by up to 90% compared to Ordinary Portland Cement. CFC, utilizing a low-calcium geopolymer binder, offers a projected lifespan in millennia, making it ideal for offshore wind farm foundations. The incorporation of basalt rebar, renowned for its threefold tensile strength compared to steel, enhances the structural integrity while being lighter and waterproof. Additionally, innovative slip-form construction allows continuous pouring of CFC, achieving production rates of up to 100 feet per day. Together, these advancements are essential for promoting renewable energy and efficient construction practices.
Construction Efficiency Techniques
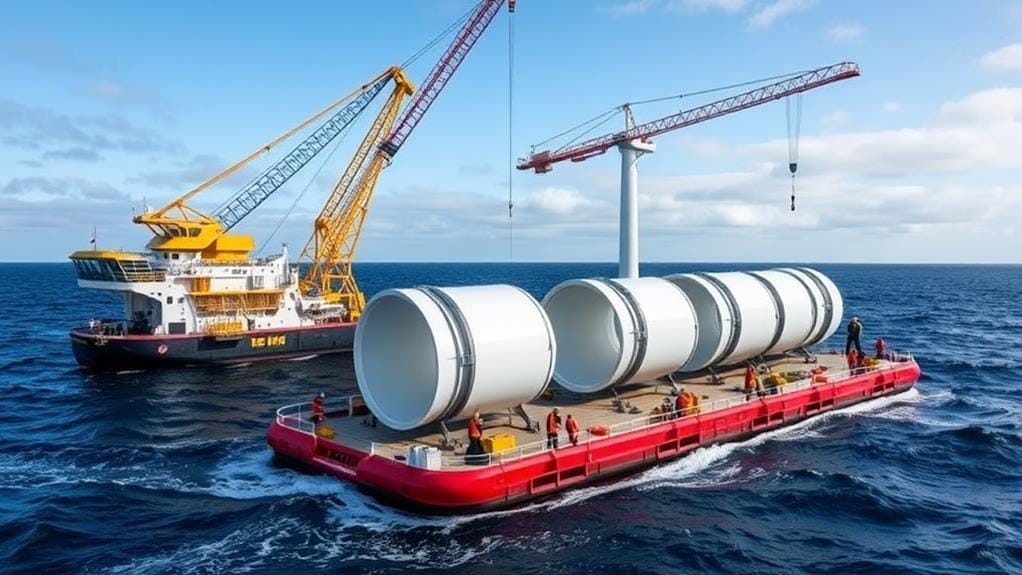
In the domain of offshore wind farm construction, employing efficient techniques can make a significant difference in project timelines and costs. By utilizing innovative down-slipform technology, we can achieve continuous pouring of Cold Fusion Concrete, resulting in the construction of large wind turbine foundations in as little as 11 workdays. This method not only accelerates the process but also eliminates the need for traditional metal construction. Furthermore, integrated systems for self-erecting towers reduce reliance on expensive crane ships, which lowers overall project costs while ensuring structural integrity for 18-MW to 20-MW generators. Additionally, advanced anchoring systems, like CFC chain/gravity and suction caisson anchors, enhance sustainability and durability, dramatically lowering capital and maintenance requirements over the structure’s lifespan.
Economic and Engineering Challenges
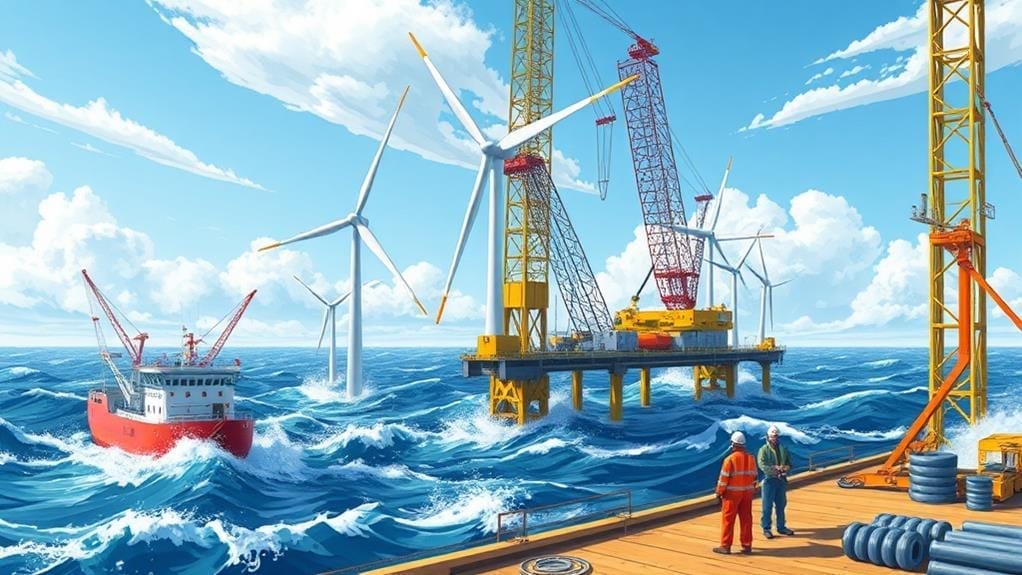
As we explore the economic and engineering challenges of offshore wind farm construction, we must consider the significant costs associated with crane ships, which are essential for assembling large wind turbine generators (WTGs) but are often limited in availability. To address these hurdles, innovative structural integrity solutions are vital; they not only aim to minimize assembly costs but also enhance the durability of installations in extreme sea conditions. By integrating advanced construction methods that reduce reliance on expensive equipment, we can improve the economic viability of these projects, potentially achieving a 40% reduction in overall expenses and paving the way for more sustainable energy solutions.
Cost of Crane Ships
Frequently, the costs associated with crane ships present significant economic and engineering challenges in the construction of offshore wind farms. These installation vessels, essential for lifting heavy wind turbine generators, are not only costly to operate but also often limited in availability, which can severely impact project timelines and budgets. To address these challenges, innovative designs that minimize reliance on crane ships are vital. For instance, integrated construction systems for self-erecting towers can potentially reduce assembly costs by at least 40%, thereby lowering overall project expenses. Additionally, U.S. naval architects and oil-and-gas engineers are focusing on solutions that mitigate extreme sea conditions, further enhancing cost efficiency associated with offshore wind installations and contributing to a more sustainable energy future.
Structural Integrity Innovations
Structural integrity innovations are vital as we tackle the economic and engineering challenges of offshore wind farm construction. With the rise of larger offshore wind turbines, innovative designs are essential to minimize assembly costs while ensuring structural integrity. U.S. naval architects and oil-and-gas engineers are developing maintenance-free foundations made from Cold Fusion Concrete, projected to last a millennium, thereby greatly reducing maintenance trips and overall costs. Additionally, integrated construction systems for self-erecting towers eliminate the need for costly crane ships, particularly for the new 18-MW to 20-MW WTGs. By utilizing advanced anchoring systems like CFC chain/gravity and suction caisson anchors, we enhance structural stability while achieving a minimum of 40% cost reduction, paving the way for a sustainable offshore wind future.
Transportation and Installation Logistics
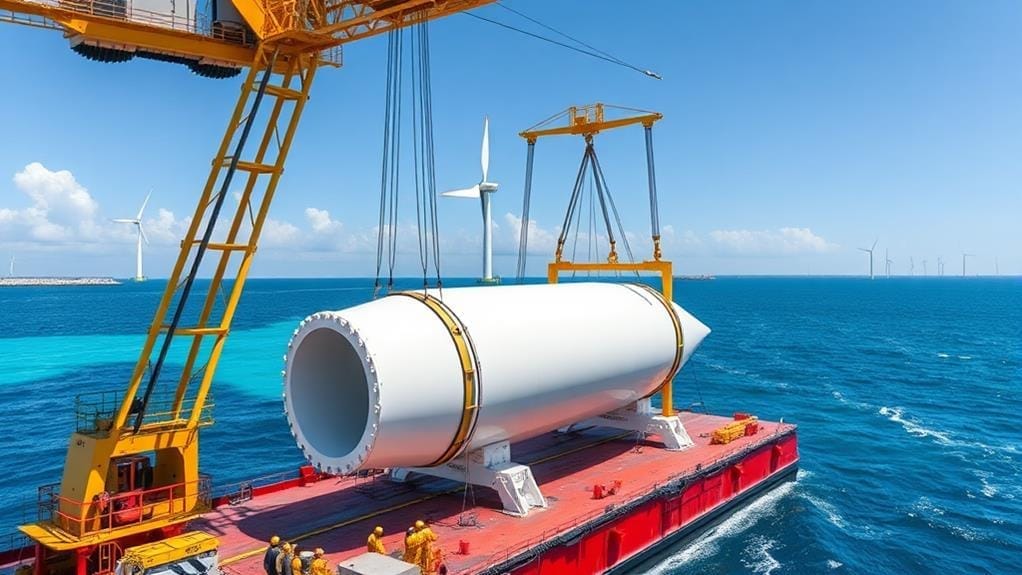
In addressing the transportation and installation logistics of offshore wind farms, we encounter significant challenges related to component delivery and the coordination of installation vessels. The large size and weight of components, such as nacelles and turbine blades, necessitate specialized transportation vessels capable of heavy lifting, while their collective transport minimizes time spent on-site. Additionally, the careful orchestration of these logistics is essential, as extreme weather conditions and port infrastructure limitations can disrupt schedules and impact the overall efficiency of the installation process.
Component Delivery Challenges
When we consider the complexities of transporting and installing offshore wind farm components, it’s clear that effective logistics are vital for project success. We face several component delivery challenges that require our attention:
- Specialized transportation logistics for large nacelles and turbine blades.
- The necessity of installation vessels equipped with cranes for precise component placement.
- Floating storage on barges before final transport, which demands efficient scheduling to mitigate weather-related delays.
- Infrastructure limitations at ports, highlighting the urgent need for upgraded facilities to handle the size and volume of these components within the marine environment.
Navigating these challenges is essential, as each factor notably impacts our timelines, safety protocols, and overall project efficiency in the development of offshore wind farms.
Installation Vessel Coordination
Proper coordination of installation vessels is essential for the timely and efficient execution of offshore wind farm projects. These specialized vessels are designed to transport heavy loads, such as pre-assembled turbine components—nacelles and blades—directly to installation sites, minimizing offshore assembly work. Effective logistics coordination is critical, as we must carefully schedule transport to accommodate unpredictable weather conditions that can greatly impact installation timelines. Additionally, we often face infrastructure limitations at ports, complicating the logistics of moving large components. During the installation process, cranes mounted on these vessels facilitate the precise placement of turbine elements, ensuring both safety and structural integrity. By mastering these logistical challenges, we can enhance the overall success of offshore wind projects.
Innovations in Offshore Wind Technology
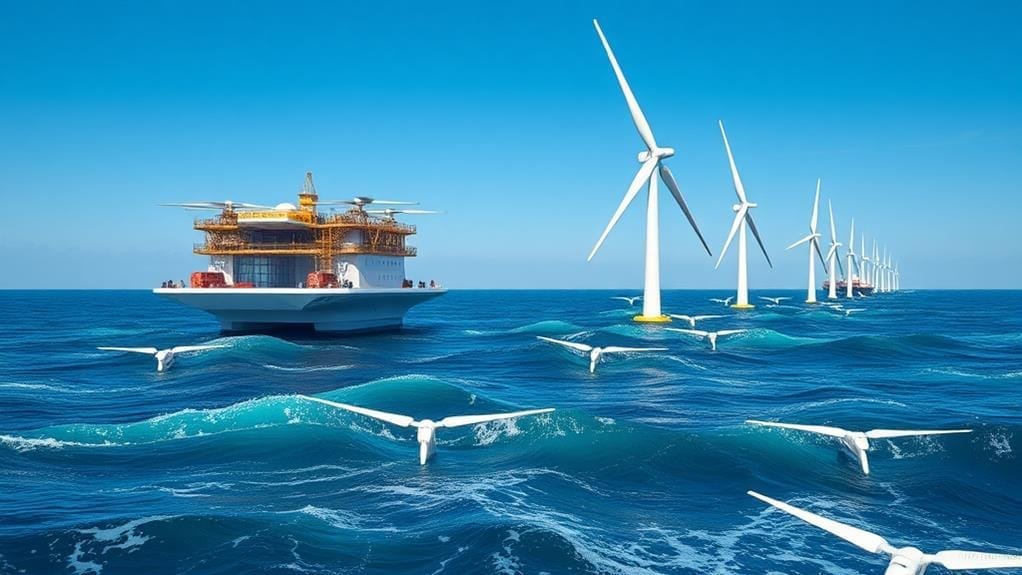
Harnessing innovative technologies is revolutionizing the offshore wind industry, paving the way for more efficient and sustainable energy production. We’re witnessing remarkable advancements that greatly enhance our capabilities, including:
- Floating foundations like semi-submersible and spar-buoy designs, which support larger 18-MW to 20-MW turbines in deeper waters.
- Cold Fusion Concrete (CFC), a groundbreaking material that reduces carbon emissions by 90% and boasts a lifespan in millennia.
- Advanced slip-form construction, enabling continuous concrete pouring at rates of up to 100 feet per day, lowering costs and production time.
- Jetting techniques, which have reduced underwater noise levels during monopile installations by 34 decibels, promoting marine life protection.
These innovations in offshore wind technology are essential for a sustainable energy future.
Marine Ecosystem Conservation Efforts
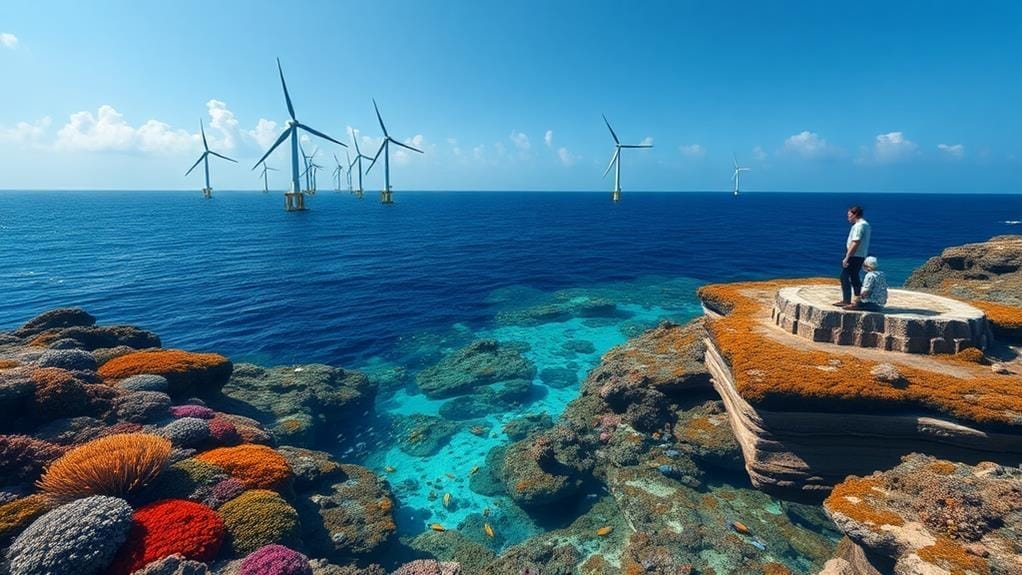
As we explore the advancements in offshore wind technology, it’s clear that we must also prioritize the health of marine ecosystems during construction. This commitment is reflected in various conservation efforts designed to protect marine life, particularly marine mammals.
Conservation Efforts | Description | Impact |
---|---|---|
Noise Control Legislation | Limits disturbing noise during drilling | Protects marine life |
Marine Mammal Protocols | Guarantees construction activities consider marine mammals | Minimizes adverse effects |
Monitoring Systems | Tracks bird and fish migration patterns | Reduces ecological impacts |
Local Community Engagement | Establishes communication with fishermen | Promotes coexistence |
Protective Measures | Implements strategies for biodiversity conservation | Safeguards overall ecosystem |
Through these initiatives, we aim for a balanced approach that harmonizes offshore wind development with the importance of our marine ecosystem.
Future Trends in Offshore Wind
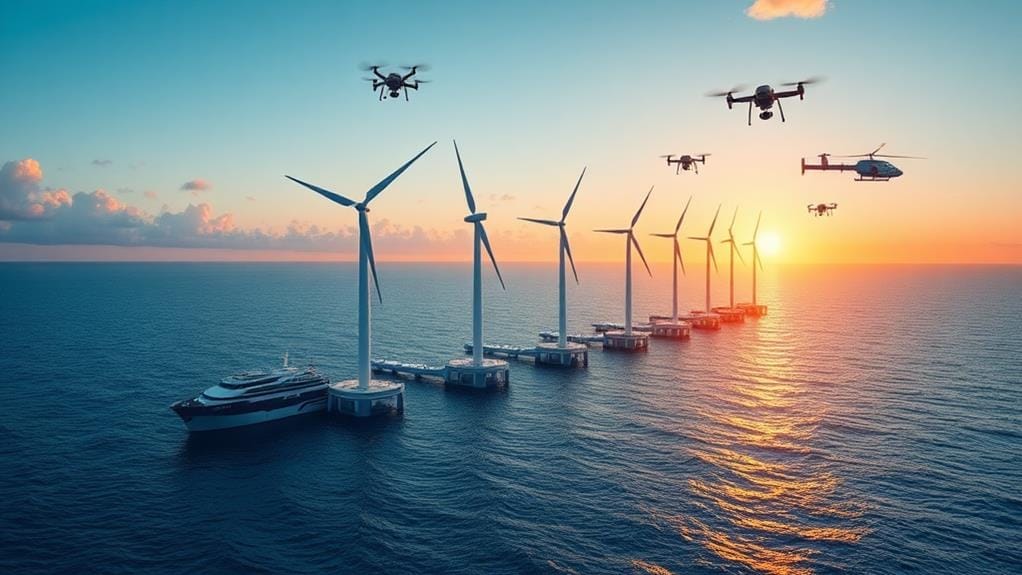
With the surge in offshore wind energy development, we’re witnessing exciting innovations that promise to reshape the industry. As we look ahead, several key trends are emerging:
- The adoption of floating foundation technologies, vital for deep-water installations, will enable access to untapped wind resources.
- Cold Fusion Concrete is paving the way for sustainable construction materials, boasting a lifespan of millennia and a 90% reduction in carbon footprint.
- Enhanced construction efficiency through slip-form techniques will allow for rapid advancements, achieving up to 100 feet of structure per day.
- Lower-noise installation methods, like patented jetting technology, are critical for marine life protections, reducing underwater noise by over 99%.
Together, these innovations will revolutionize how we approach offshore wind farm construction.
Frequently Asked Questions
What Is the New Technology for Offshore Wind?
We’re excited about new technologies transforming offshore wind! Floating turbines, advanced materials, and energy storage enhance efficiency, while installation vessels and digital monitoring minimize environmental impact, ensuring seamless grid integration for a sustainable future together.
What Is Currently the Most Used Offshore Wind Foundation Type?
When we consider offshore wind foundations, we see monopile foundations dominating, jacket structures emerging, floating platforms innovating, gravity foundations stabilizing, hybrid systems evolving, and suction buckets enhancing installation techniques. Together, we’re shaping a sustainable energy future.
What Are the Different Types of Offshore Wind Structures?
When exploring offshore wind structures, we see various types like floating platforms, monopile designs, jacket structures, gravity bases, tension legs, and hybrid systems, alongside exciting substation innovations that advance our collective pursuit of sustainable energy solutions.
How Do Offshore Wind Farms Get Built?
Building offshore wind farms involves complex installation logistics, site selection, and workforce training. We must navigate regulatory challenges, consider project financing, and implement maintenance strategies while minimizing environmental impact to create sustainable energy solutions together.