To enhance wind turbine efficiency, we must prioritize three critical maintenance practices: regular inspections, preventive maintenance strategies, and thorough documentation. Conducting inspections every 4-6 months allows us to identify wear, cracks, and corrosion on key components such as blades, nacelles, towers, and generators. Implementing routine lubrication and condition-based maintenance schedules can optimize operational reliability, potentially decreasing unplanned downtimes by up to 30%. Additionally, maintaining meticulous records guarantees compliance with safety standards and aids in forecasting future maintenance needs, ultimately supporting a sustainable future for wind energy systems. We can explore further strategies to optimize our maintenance approach.
Key Takeaways
- Conduct regular inspections every 4-6 months to identify wear, cracks, or corrosion early on and prevent major failures.
- Implement predictive maintenance techniques to utilize real-time data and reduce unplanned downtimes by up to 30%.
- Lubricate bearings and gearbox components routinely to mitigate wear and enhance the longevity of turbine parts.
- Keep detailed records of all inspections and repairs to track operational history and forecast future maintenance needs.
- Utilize advanced monitoring systems for real-time health assessments, optimizing maintenance scheduling and improving efficiency.
Regular Inspections and Monitoring
When we think about maintaining wind turbines, regular inspections and monitoring are essential to ensuring their efficiency and longevity. Conducting regular inspections every 4-6 months helps us identify potential issues, preventing unexpected breakdowns. During these inspections, we focus on key components like blades, nacelle, tower, and generator, looking for signs of wear, cracks, or corrosion. Advanced monitoring systems provide real-time health assessments, enabling us to implement condition-based maintenance that optimizes scheduling. Utilizing predictive maintenance techniques, we can analyze performance data to forecast potential failures, greatly reducing unplanned downtimes by up to 30%. Documenting inspection findings and maintenance activities is crucial for compliance and tracking operational history, ultimately contributing to enhanced efficiency and safety in our wind turbine operations.
Preventive Maintenance Strategies
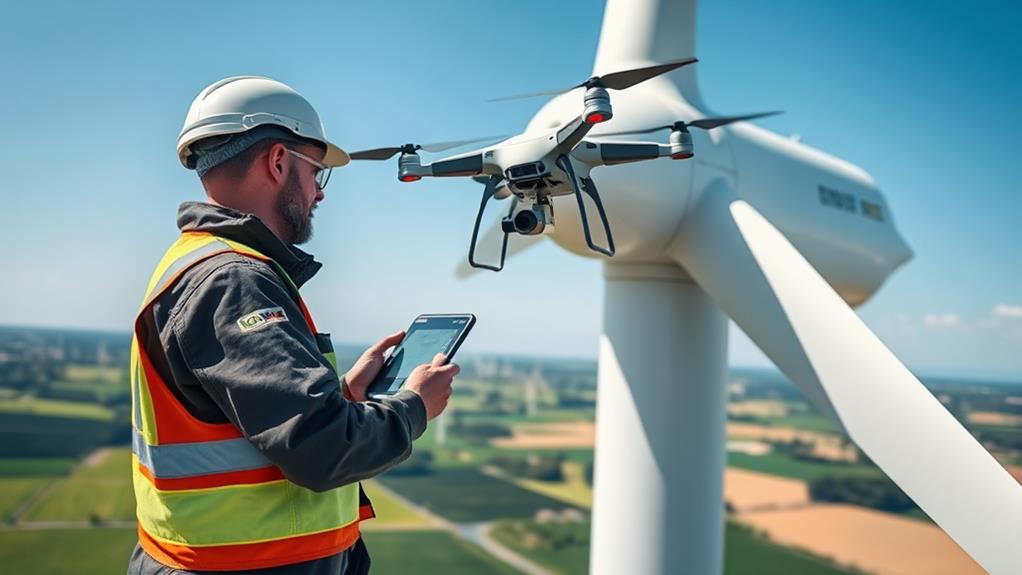
To maintain ideal performance and extend the lifespan of our wind turbines, we must prioritize preventive maintenance strategies. By implementing routine inspections every 4-6 months, we can identify potential issues early, effectively reducing unplanned downtimes by up to 30%, ultimately enhancing operational efficiency. Key preventive tasks include regular lubrication of bearings and gearbox components, essential for mitigating wear and tear, ensuring smooth turbine operation. Additionally, adopting condition-based maintenance allows us to utilize real-time data, optimizing our maintenance scheduling, which enhances reliability and turbine performance. By focusing on these preventive maintenance activities, we not only improve our turbines' operational capabilities but also align with industry standards and compliance requirements, securing a sustainable future for our wind energy initiatives.
Documentation and Compliance
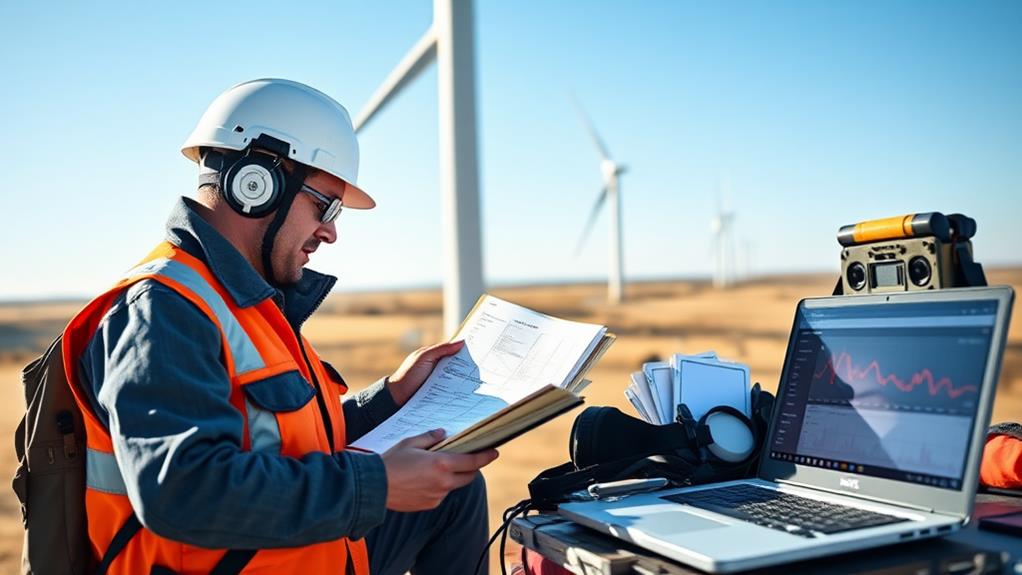
Effective documentation and compliance are essential components of wind turbine maintenance that we can't overlook. Regularly maintaining detailed records of inspections, repairs, and parts replacements not only tracks our operational history but also guarantees compliance with safety standards and industry regulations. It's vital that we keep safety documentation accessible and updated, especially after personnel changes or modifications to protocols. Using digital platforms can enhance our documentation processes, allowing for real-time updates and streamlined audits to verify compliance. Furthermore, maintaining thorough maintenance records helps us identify trends and forecast future maintenance needs, ultimately improving system reliability and longevity. Adhering to these practices safeguards our operations and supports a culture of safety and efficiency in our industry.
Frequently Asked Questions
How to Make Wind Turbines More Efficient?
We can't overlook that efficiency isn't just about maintenance. By focusing on blade design, aerodynamic optimization, control systems, and performance monitoring, we'll harness technological advancements and smart site selection for a sustainable energy future together.
What Maintenance Does a Wind Turbine Need?
When we think about wind turbine maintenance, we can't forget blade inspections, gearbox lubrication, and electrical checks. Regular performance monitoring, bearing maintenance, and safety protocols, like vibration analysis and pitch adjustment, keep our turbines running smoothly.
What 3 Main Factors Determine the Efficiency of a Wind Turbine?
Imagine a ship sailing smoothly through the wind; we believe turbine efficiency hinges on blade design, site selection, and generator performance. Together, let's harness wind speed, control systems, and material quality for maximum energy output.
What Are the Maintenance Intervals for Wind Turbines?
When we consider maintenance intervals for wind turbines, we're looking at preventive maintenance like turbine inspections, oil changes, and gearbox checks. Regular performance monitoring and seasonal preparations, alongside safety protocols, guarantee smooth operation and reliability.