We recognize the advancements in vertical axis wind turbines (VAWTs) that focus on maximizing performance through innovative designs and flow control techniques. Darrieus turbines can achieve power coefficients near 0.40, while Savonius rotors reach a maximum of 0.31. Recent innovations, such as plasma actuators and synthetic jets, enhance aerodynamic efficiency, increasing energy capture by up to 13.37%. Additionally, computational fluid dynamics (CFD) has validated improvements in blade design and dynamic control systems, which enable real-time adjustments. These advancements collectively enhance sustainability and operational efficiency, underpinning a significant potential for growth in VAWT technology that is worth exploring further.
Key Takeaways
- Vertical Axis Wind Turbines (VAWTs) utilize simple designs and are insensible to wind direction, improving installation efficiency in urban areas.
- Advancements such as leading edge tubercles and plasma actuators enhance the aerodynamic performance and increase power coefficients significantly.
- Hybrid designs and counter-rotating VAWTs can double energy output and improve performance, especially in low wind conditions.
- Computational Fluid Dynamics (CFD) simulations provide critical insights into turbine design optimization and validate performance enhancements against experimental data.
- Sustainable VAWT designs minimize environmental impact by reducing land occupation and improving energy capture at low wind speeds.



Overview of Vertical Axis Wind Turbines
When it comes to harnessing wind energy, Vertical Axis Wind Turbines (VAWTs) offer unique advantages that make them appealing for various applications. With designs like the Darrieus and Savonius turbines, we can effectively capture energy through aerodynamic lift and drag, respectively. Their simple design allows for ease of installation, especially in urban environments, where they remain insensitive to wind direction, eliminating the need for costly yaw mechanisms. While the efficiency of VAWTs can be lower than Horizontal-Axis Wind Turbines, advancements such as innovative flow control techniques are enhancing their aerodynamic performance. These improvements have the potential to boost power coefficients by up to 13.37%, making VAWTs increasingly competitive among renewable energy sources. Together, we can explore these fascinating developments.
Key Performance Metrics
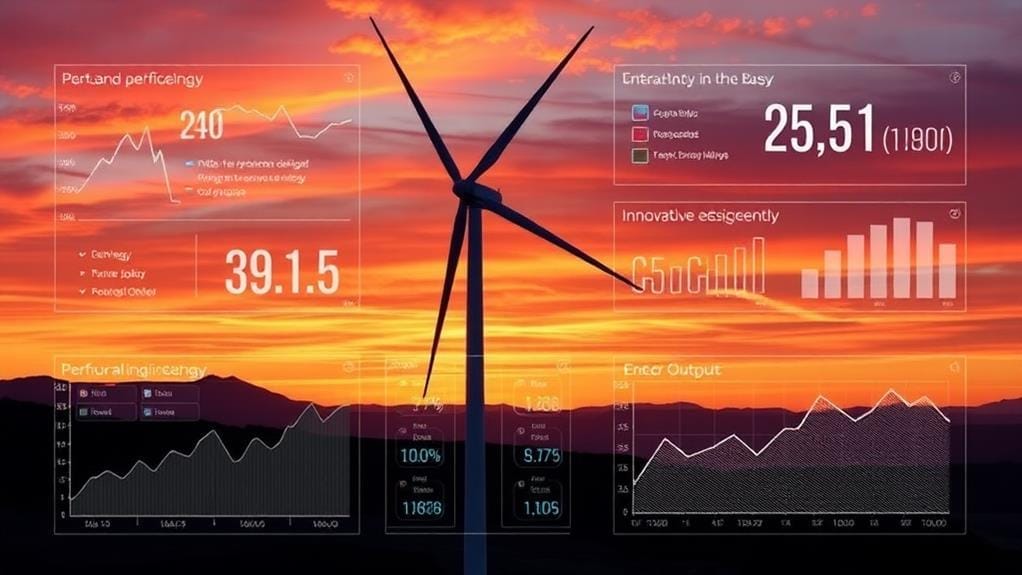
Key performance metrics play an essential role in evaluating the effectiveness of Vertical Axis Wind Turbines (VAWTs). The power coefficient (Cp) is vital, with innovative designs achieving impressive values of 0.475 at ideal tip speed ratios (TSR) of around 3. Darrieus turbines typically peak near 40% efficiency, while Savonius rotors max out at about 31%, highlighting the performance disparities among designs. Blade design modifications, such as leading edge tubercles (LET), can reduce drag by 32% and markedly enhance aerodynamic efficiency. In addition, ideal rotor configurations, including hybrid designs that combine Darrieus and Savonius features, can improve performance metrics in low wind conditions. Thorough CFD simulations, coupled with experimental wind tunnel testing, are essential for accurately evaluating and validating these innovations in energy conversion.
Flow Control Innovations
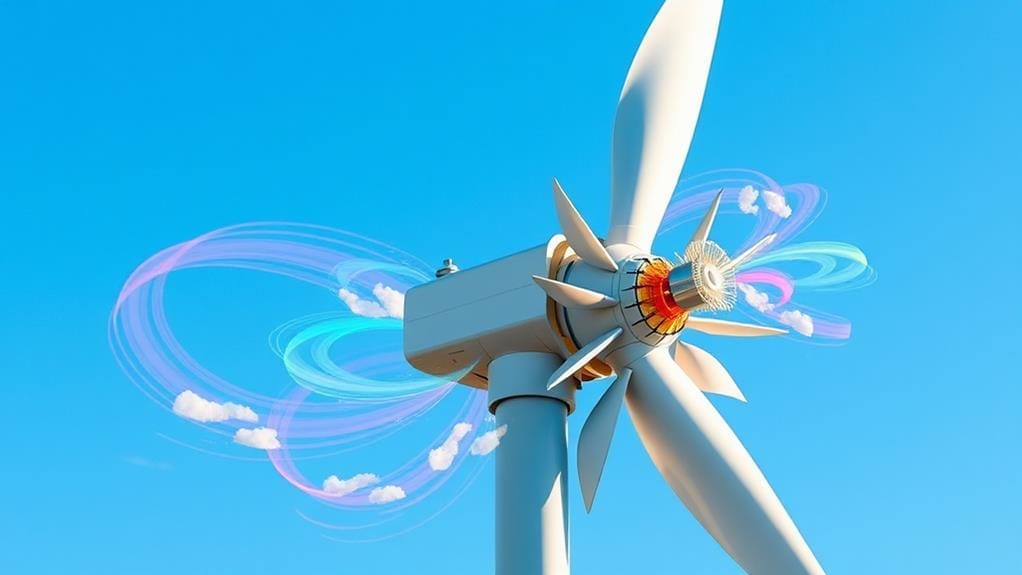
Building on our understanding of performance metrics, flow control innovations are reshaping the efficiency landscape of Vertical Axis Wind Turbines (VAWTs). By implementing advanced techniques, we can markedly enhance aerodynamic efficiency and mitigate issues like dynamic stall. Here are some key innovations we’re excited about:
- Plasma actuators and deflector plates have shown a 13.37% increase in power coefficient by optimizing airflow around blades.
- Synthetic jets considerably improve aerodynamic efficiency, effectively reducing dynamic stall.
- Leading edge tubercles (LET) achieve up to 32% less drag, promoting smoother airflow and delaying stall.
- Computational fluid dynamics (CFD) validates various tailored actuator configurations, enhancing performance under diverse wind conditions.
Together, these advancements in flow control bring us closer to maximizing the potential of VAWTs.
Numerical Simulation Techniques
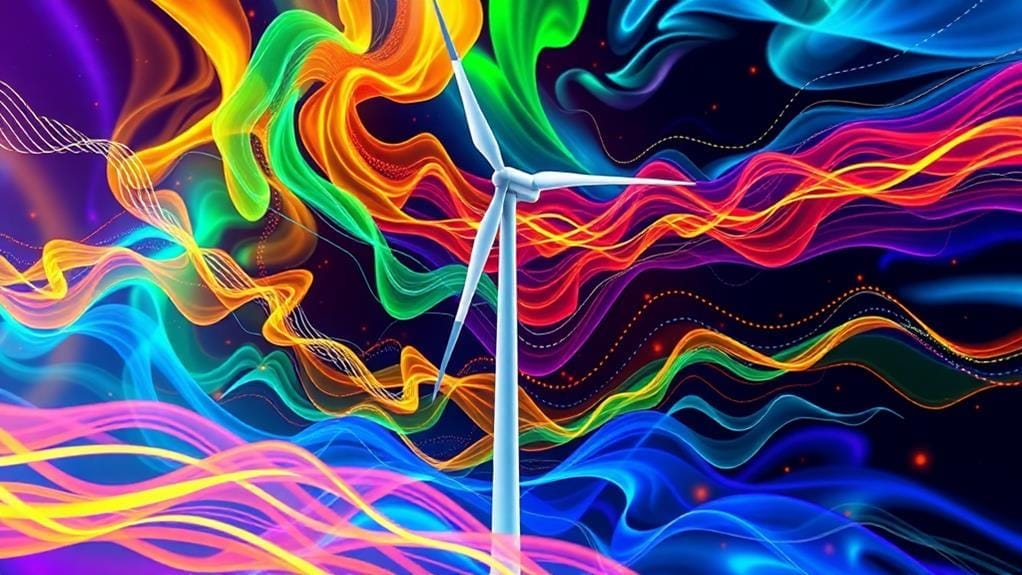
In this section, we’ll explore the essential numerical simulation techniques that underpin the design and optimization of vertical-axis wind turbines. By employing methodologies such as computational fluid dynamics (CFD), we can accurately predict the aerodynamic behavior of these turbines, utilizing models like the SST k-omega turbulence model to enhance performance validation. Additionally, we’ll discuss the significance of systematic testing through two-dimensional simulations, which allow us to evaluate various configurations and improve turbine efficiency based on reliable data.






Simulation Methodologies Overview
As we explore the simulation methodologies for vertical-axis wind turbines (VAWTs), it’s evident that numerical simulation techniques play a pivotal role in understanding their aerodynamic performance. These methodologies not only help in predicting the aerodynamic behavior but also enhance our grasp of VAWT advancements. Key elements include:
- Computational Fluid Dynamics (CFD): A cornerstone for analyzing flow characteristics.
- SST k-omega Turbulence Model: Commonly employed to assess flow behavior around VAWT designs.
- Data Curation: Thorough processes guarantee the reliability of findings.
- Optimal Actuator Configurations: Two-dimensional simulations facilitate the identification of configurations for improved performance predictions.
Computational Fluid Dynamics
The importance of computational fluid dynamics (CFD) in the analysis of vertical-axis wind turbines (VAWTs) can’t be overstated. Through CFD studies, we gain critical insights into performance enhancement, utilizing the SST k-omega turbulence model to accurately capture flow dynamics. This model enhances our predictions regarding the power coefficient, guiding systematic testing of various actuator configurations. Particularly, innovative designs featuring leading edge tubercles have demonstrated significant drag reduction and lift improvements, ultimately enhancing turbine efficiency. By employing extensive numerical simulations, we can identify ideal designs that maximize performance, ensuring that our advancements in VAWTs are both efficient and reliable. Validation of our CFD results against experimental data further solidifies our findings, supporting the development of superior VAWT designs.
Performance Validation Techniques
Building on the insights gained from computational fluid dynamics (CFD), we recognize that performance validation techniques play a pivotal role in confirming our numerical predictions. By systematically comparing our CFD simulations against experimental data, we can ascertain the accuracy of our assessments regarding aerodynamic behavior and power coefficients. Utilizing the SST k-omega turbulence model enhances our simulations, allowing us to explore various actuator configurations effectively. To facilitate our validation process, we rely on:
- Wind tunnel experiments as benchmarks for numerical results,
- Systematic testing of actuator configurations to improve power coefficients,
- Guidelines for azimuthal increments and domain sizes to enhance prediction accuracy,
- Robust performance assessments that inform necessary design modifications.
Together, these methods solidify our understanding and optimization of VAWT performance.
Experimental Validation Methods
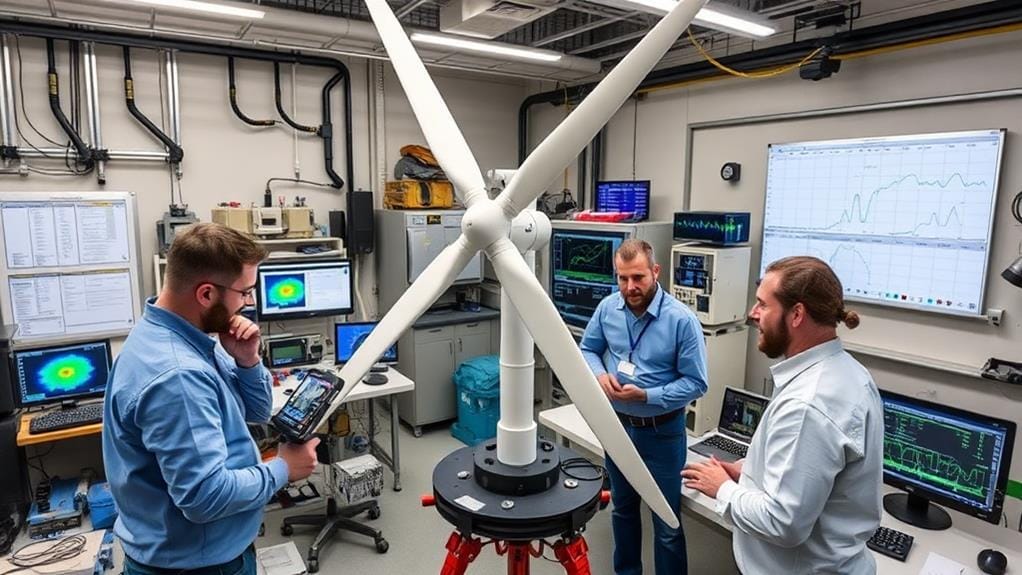
Experimental validation methods play a crucial role in advancing vertical-axis wind turbine (VAWT) technology. These methods, such as wind tunnel testing, provide critical data on aerodynamic performance and efficiency under controlled conditions. Using advanced computational fluid dynamics (CFD) tools like ANSYS Fluent, we can simulate flow behavior and validate our experimental results against numerical predictions. Scaled-down models of hybrid VAWTs allow us to assess performance metrics, including power coefficients and torque output, across various operating conditions. Remarkably, integrating features like leading edge tubercles has demonstrated up to a 32% drag reduction, enhancing aerodynamic efficiency and turbine performance. Continuous performance monitoring during these experiments guarantees our findings accurately reflect the VAWT’s operational efficiency, ultimately guiding future design optimizations and innovations.
Design Optimization Strategies
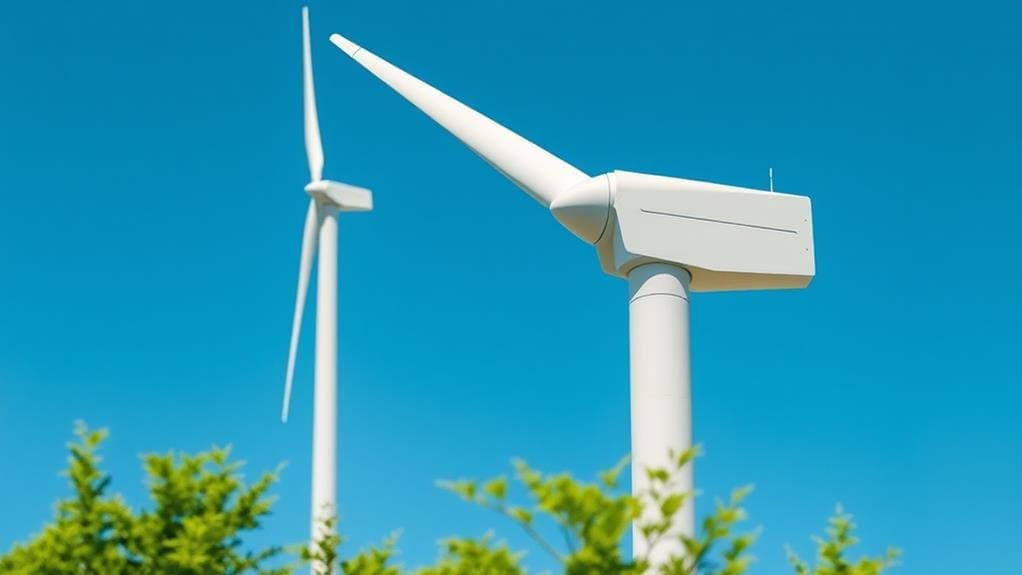
Advancements in experimental validation have paved the way for innovative design optimization strategies in vertical-axis wind turbines (VAWTs). By focusing on key methods, we can greatly enhance performance and efficiency. Here are four critical strategies we’ve identified:
- Leading Edge Tubercles (LET): These features reduce drag by 32%, enhancing aerodynamic efficiency and delaying stall.
- Computational Fluid Dynamics (CFD): This technology helps validate hybrid designs, achieving a power coefficient of 0.475 at a tip speed ratio of 3.
- Dynamic Control Systems: These systems facilitate real-time adjustments in blade pitch, optimizing energy capture across varying wind speeds.
- Bioinspired Designs and Advanced Materials: Utilizing materials like carbon nanotubes increases structural efficiency, improving interlaminar shear strength by 30%.
Together, these strategies drive performance improvements in VAWTs, ensuring a sustainable energy future.
Future Trends in VAWT Technology
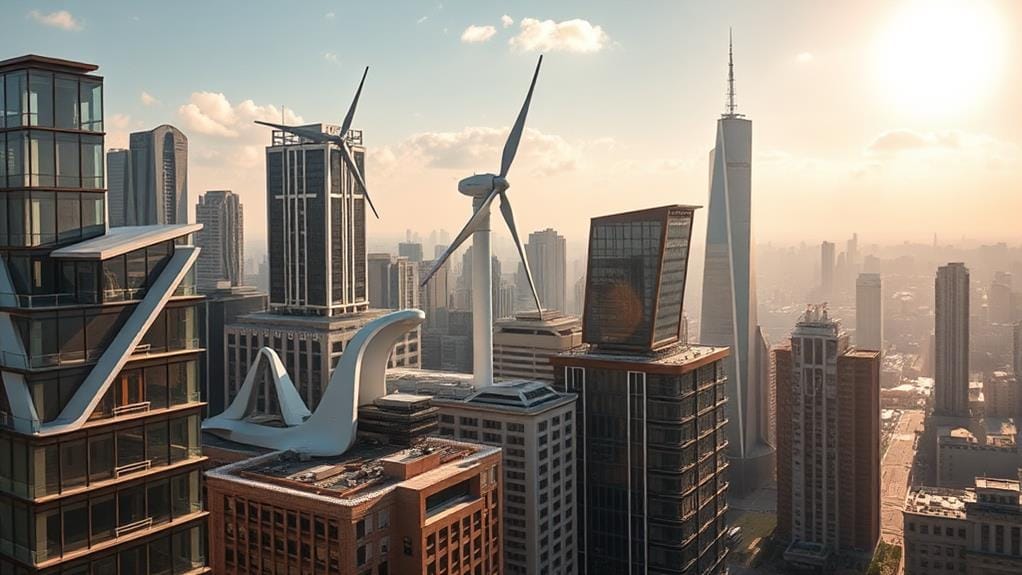
As we look ahead, the future of Vertical-Axis Wind Turbine (VAWT) technology promises exciting innovations that could reshape the renewable energy landscape. We’re poised to witness advancements in flow control methods, including plasma actuators and deflector plates, which can maximize energy capture and enhance efficiency by up to 13.37%. Additionally, counter-rotating VAWTs (CRVAWTs) have shown the potential to double output compared to traditional designs. The integration of leading edge tubercles can further improve performance by reducing drag by 32%. Advanced materials, such as ultra-high performance concrete and carbon nanotube composites, will enhance structural integrity. Furthermore, machine learning algorithms will optimize real-time control, improving predictive capabilities and facilitating better integration with renewable energy grids, ultimately driving us toward a more sustainable future.
Environmental Impact and Sustainability
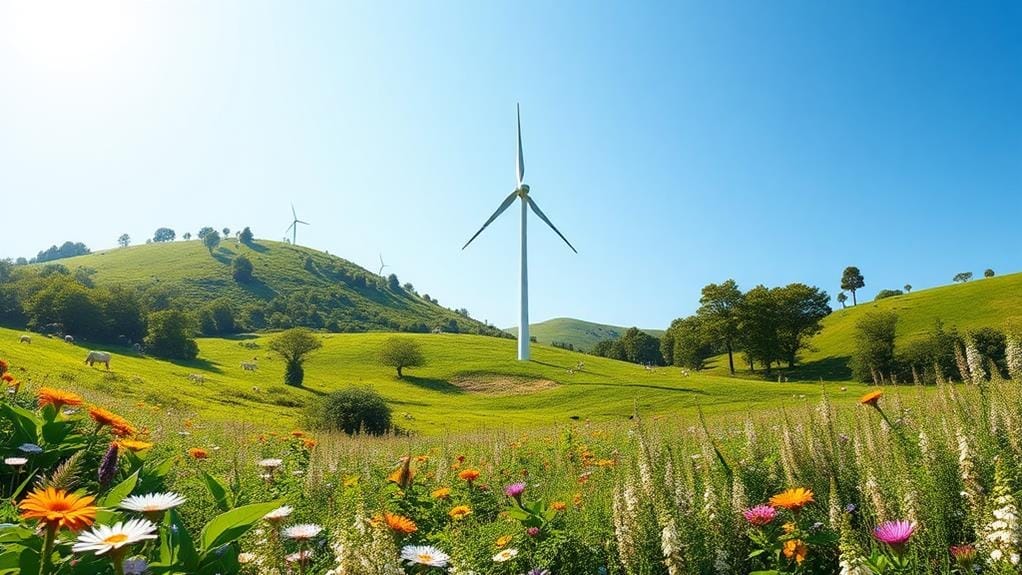
Vertical Axis Wind Turbines (VAWTs) present a unique opportunity for enhancing environmental sustainability in renewable energy. Their design allows for efficient operation in urban environments, considerably reducing their environmental impact compared to traditional turbines. By employing advanced VAWT technology, we can achieve better energy capture and less aerodynamic losses through innovative flow control techniques. Here are some key benefits of VAWTs:
- Improved performance at low wind speeds, broadening renewable energy accessibility.
- Integration of advanced materials, which leads to lighter structures and reduced manufacturing energy consumption.
- Reduced habitat disruption, as fewer turbines can achieve equivalent capacity.
- Minimal land occupation, preserving more natural spaces for local ecosystems.
Through these advancements, we’re promoting sustainability, ensuring a better future for our planet.
Frequently Asked Questions
How Can We Increase the Efficiency of VAWT?
To increase VAWT efficiency, we can focus on blade design and airflow optimization, choose suitable materials, optimize turbine height, apply effective maintenance techniques, and consider energy storage and noise reduction strategies while evaluating environmental impact and cost analysis.
Are Vertical-Axis Wind Turbines Really the Future?
As we envision a skyline dotted with sleek, hybrid vertical-axis wind turbines, we can’t help but wonder: could they conquer urban applications? With noise reduction, aesthetic design, and community acceptance, the future looks promising yet challenging.
What Is the Most Efficient VAWT Design?
When we think about the most efficient VAWT design, we consider drag design, lift design, and hybrid systems. Material innovation and scale optimization enhance urban applications, while noise reduction and maintenance strategies guarantee cost-effective energy storage solutions.
How Can You Increase the Efficiency of a Wind Turbine?
Imagine harnessing the wind’s whispers—by refining blade design, embracing aerodynamic improvements, choosing the right materials, and optimizing maintenance practices, we can elevate efficiency, reduce noise, and enhance our collective environmental impact while ensuring energy storage reliability.