When examining the three key materials for wind turbine blades—fiberglass, aluminum, and composites—we find that each offers distinct pros and cons. Fiberglass is lightweight and cost-effective, optimizing energy capture but suffers from durability issues. Aluminum provides exceptional durability, resisting winds up to 75 mph while being corrosion-resistant; however, its initial cost can be higher. Composites, particularly carbon fiber, offer superior strength-to-weight ratios and performance enhancements, yet they may incur higher costs and quality control challenges. Understanding these characteristics is essential for optimizing turbine design and functionality; further insights can help enhance our decision-making process.
Key Takeaways
- Fiberglass Blades: Lightweight and cost-effective but prone to cracking and requires regular maintenance due to weather-related erosion.
- Aluminum Blades: Highly durable, corrosion-resistant, and stable, offering long-lasting performance with reduced maintenance needs.
- Composite Materials: Provide a strong strength-to-weight ratio, enhancing energy capture, though they may suffer from quality control issues and higher costs for carbon fiber.
- Fiberglass vs. Aluminum: Fiberglass is cheaper but less durable, while aluminum offers greater longevity and stability in harsh conditions.
- Maintenance Considerations: Regular upkeep is essential for fiberglass blades, whereas aluminum typically requires less maintenance over the turbine’s lifespan.



Fiberglass Blade Advantages and Disadvantages
When we consider fiberglass blades for wind turbines, we find a mix of advantages and disadvantages. These blades are lightweight, which makes them suitable for small wind generators and widely used in industrial turbines due to their cost-effective nature. Their good strength-to-weight ratio allows for longer blades, enhancing energy capture. However, low production quality can lead to structural issues like cracking and breaking under stress, resulting in increased long-term replacement costs. While fiberglass offers decent durability, it pales in comparison to higher-end materials like carbon fiber. Regular maintenance is essential, as fiberglass blades are prone to weather-related erosion and damage, which can negatively affect performance and incur hidden costs for DIY wind generator owners.
Benefits and Drawbacks of Aluminum
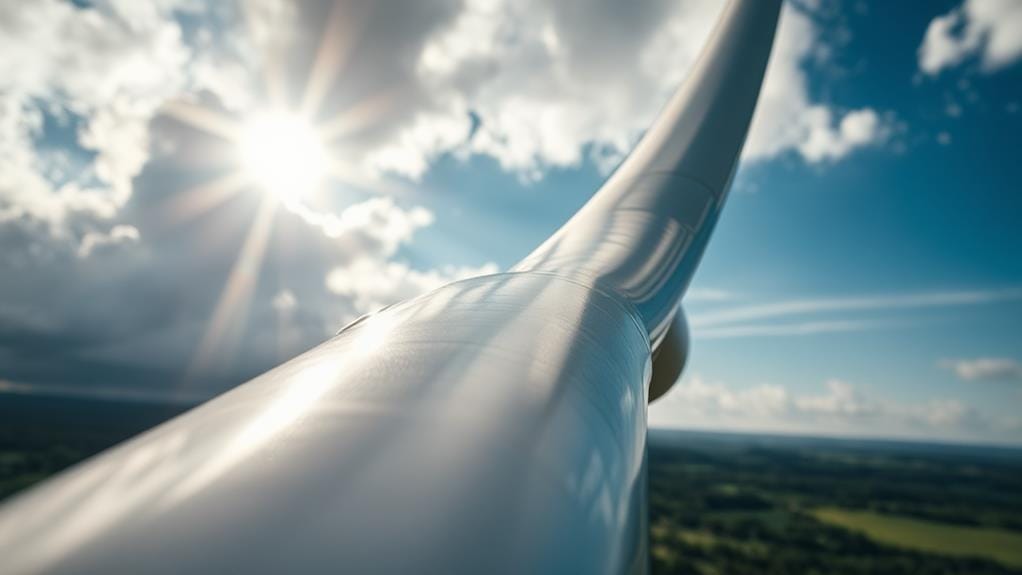
While fiberglass blades have their merits, aluminum offers a compelling alternative for wind turbine construction. We can appreciate the benefits of aluminum blades, particularly their:
- Durability: Capable of withstanding winds up to 75 mph, they excel in various environmental conditions.
- Corrosion Resistance: Crafted from aircraft-grade aluminum alloys, they resist corrosion without needing protective coatings.
- Stability: Although heavier than synthetic materials, this weight enhances stability, preventing warping or bending over time.
- Cost-Effectiveness: Their long-lasting performance reduces maintenance requirements, ultimately saving costs over the wind turbine’s operational lifespan.
Pros and Cons of Composite Materials
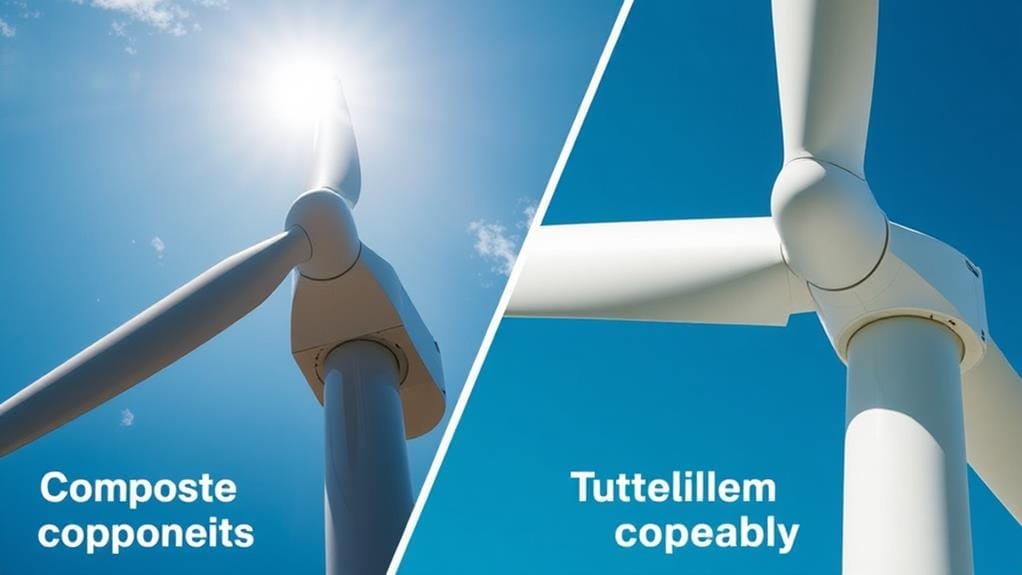
Exploring the pros and cons of composite materials reveals their significant impact on wind turbine blade design. Composite materials, such as fiberglass and carbon fiber, boast a high strength-to-weight ratio, enabling the creation of longer blades that enhance energy capture efficiency. While fiberglass is cost-effective and lightweight, it can face structural issues if low-quality manufacturing processes are employed, potentially compromising durability. On the other hand, carbon fiber, though pricier, offers superior tensile strength and flexural capabilities, making it suitable for high-stress areas of turbine blades. Additionally, hybrid composites, which combine materials like E-glass and carbon fibers, are emerging to optimize both performance and cost. Enhanced manufacturing processes, such as vacuum infusion, further improve quality control and reduce defects in production.






Frequently Asked Questions
What Is the Best Material for Wind Turbine Blades?
They say, “You get what you pay for.” For wind turbine blades, we believe composite materials like fiberglass and carbon fiber balance strength, durability, and cost efficiency, enhancing performance longevity while addressing maintenance challenges and environmental impact.
What Is the Best Material for a Gas Turbine Blade?
When considering the best gas turbine blade materials, we should explore high temperature alloys and ceramic composites. Their advanced coatings and manufacturing processes enhance fatigue resistance, performance optimization, and reduce environmental impact, balancing cost analysis effectively.
What Is the Most Effective Wind Turbine Blade Design?
Did you know some wind turbine blades stretch over 351 feet? We find that aerodynamic efficiency, pitch control, and innovative manufacturing techniques enhance performance optimization, while considering cost analysis, maintenance requirements, and environmental impact guarantees our sustainable future.
What Materials Are Used in Turbine Blades?
We recognize the importance of materials in turbine blades, like composite materials that enhance structural integrity and aerodynamic performance. By optimizing weight distribution and cost efficiency, we can also improve blade longevity and repair techniques, reducing environmental impact.